Gasketed Plate Heat Exchangers
Gasketed plate heat exchangers are used in many processes, in all kinds of industries. Auxiliary cooling at a power generation plant, or wort cooling at a brewery, or an ammonia evaporator to produce chilled water for mineshaft cooling are all applications done by plate type heat exchangers.
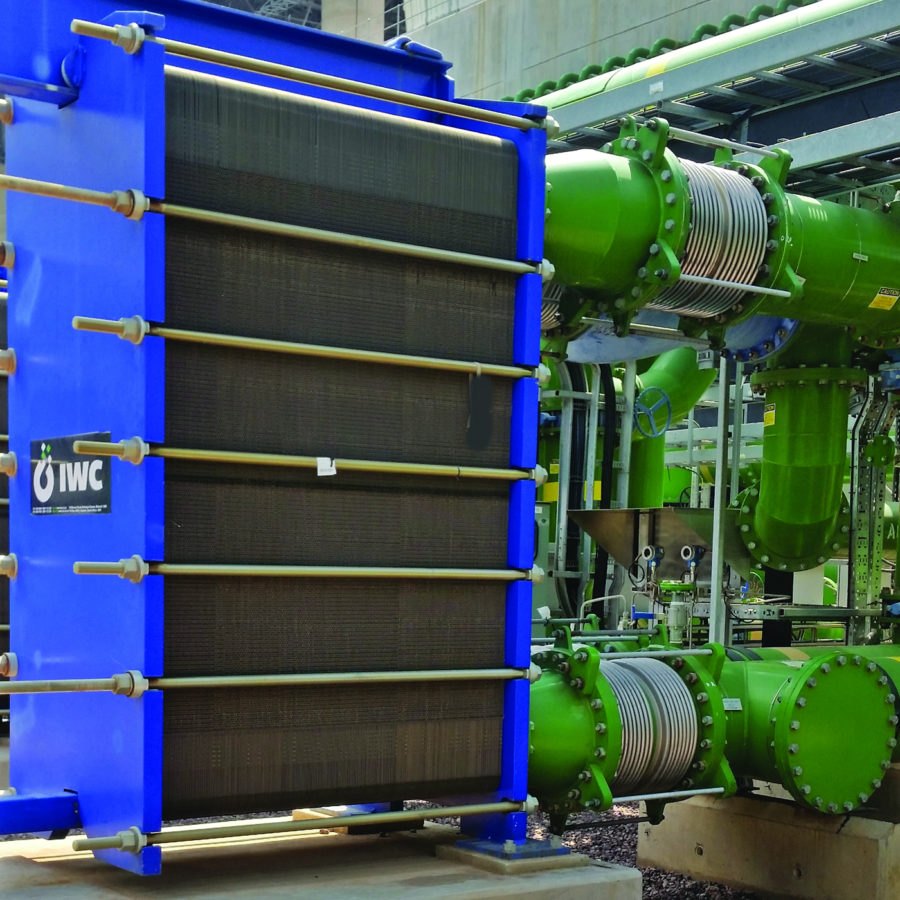
Components
Frame
The frame of a Plate Heat Exchanger is designed for industrial application and made of Carbon Steel and coated with a Poly-urethane paint. Tightening bolts are fitted on each side of the frame to clamp the plate pack to the correct tightening size.
For hygienic or corrosive environments, the frame can be manufactured in solid or cladded 304L / 316L stainless steel.
Connections
The Inlet and Outlet connections for both the hot and cold sides are made to ANSI or DIN standards but can also be made to other standards. Connections can be lined with either rubber or in the same material as the plates. An option of Studded or Weld Neck Flanges are available.
Plates
For standard applications, such as water to water, or water to oil heating/ cooling, we use 304SS or 316SS plate material. Chloride content and operating temperature needs to be considered when making the plate selection. Chlorides of 150-200ppm at 40ºC is the recommended limit. A more exotic material is advisable if chloride concentration and/or temperatures are higher. Materials such as Titanium, SMO254, Nickel and Hastelloy C276 are used for more aggressive applications.
Gaskets
The standard material for gaskets is Nitrile (NBR) and EPDM. These are used for most applications, for acids, ammonia, etc. gasket materials such as Viton and Neoprene are used.
Advantages
Cost effective, small footprint and light weight compared to Shell & Tube HE’s
Very close temperature approach achievable, up to 1 degree Celsius
Flexible design. Plates can be added or removed to compensate for production changes. In case of compromised plates (pinholes or cracks), these can easily be removed and replaced with new ones
Low energy consumption due to low hold up volumes and quick response to process fluctuations
Easy to maintain
Compact and light design results in simple, economical installation
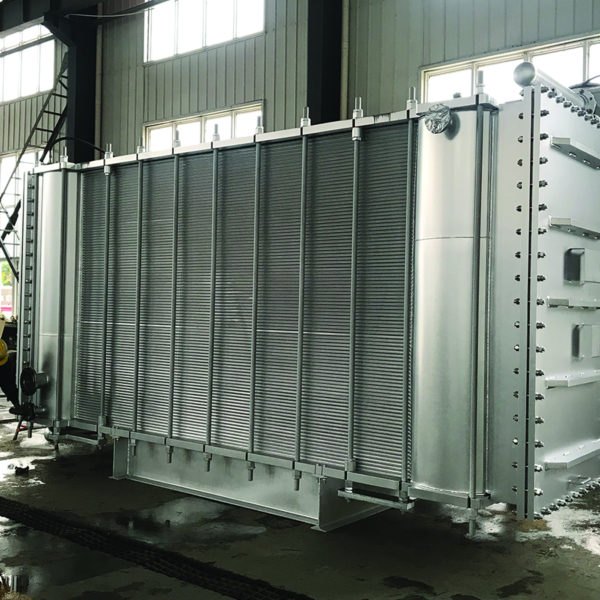