The A-Z of SX-EW – Engineered thermal solutions for all cooling tower needs
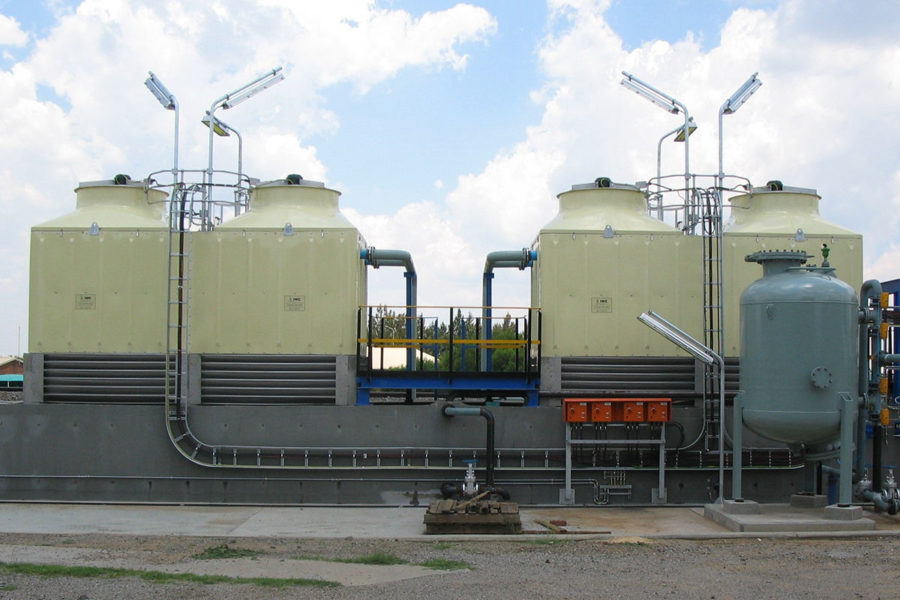
Well-known throughout southern Africa as a cooling tower specialist, Industrial Water Cooling (IWC) provide cooling tower and heat exchanger solutions to mines in the Democratic Republic of the Congo (DRC) and Zambia. While the DRC exports cobalt, tantalum and tin worldwide, Zambia is too, a mineral-rich landscape and both form a crucial part of Africa’s Copperbelt.
In the mining sector, solvent extraction (SX) and electro winning (EW) – a two-stage hydrometallurgical process – is best practise due to the fact that heat generated by SX-EW plant processes must either be rejected or harnessed and then transferred back into the system.
In the electrowinning process, electric current is used to plate out the copper into copper cathodes. All water used through this process is treated and recycled back into the extraction process. Along with its wholly-owned subsidiary, Tektower, IWC provides world-class thermal solutions and water cooling towers to do this.
Here’s how it works:
Cooling Towers
Cooling towers make up the very heart of a plant cooling system. They provide the necessary heat rejection for SX-EW plants to operate both effectively and efficiently. Dependant on the design conditions and required processes, cooling towers can either be smaller, factory-assembled package types, or large, field-erected cooling towers.
“Given the corrosive environments of SX-EW plants, cooling towers need to be robust to ensure the maximum return on a mine’s CAPEX spend,” says Deon Fawell, IWC’s Sales and Marketing Manager. “Operation and maintenance costs – competitively-priced, readily available cooling tower spare parts for example – impact a mine’s OPEX spend.”
Continuous preventative (and in-depth) maintenance is key to ensure that cooling towers deliver on design, performance and duty. As a procurement manager, you’ll need to ensure that cooling towers meet the required duty and adhere to plant specifications.
Along with your engineering and maintenance teams, it’s important to understand and ask:
- Are spare parts readily available?
- Can they be sourced locally, or will we need to import spare parts from abroad?
- Is the full tower specification and spare parts list easily available and fully accessible to the end user?
Heat Exchangers
To harness and transfer heat generated during SX processes back into the system, heat exchangers are essential with gasketed and welded plate heat exchangers known to be the most efficient technology for heat transfer. These types of heat exchangers offer a large heat transfer area, close temperature design and are 90% smaller than shell-and-tube heat exchangers.
“Additionally, plate heat exchangers are low-cost and low maintenance,” says Fawell.
Understanding the SX-EW Process
In the SX process, plate heat exchangers are used to control chemical temperatures where crushed copper ore is leached with sulphuric acid to produce impure solutions of copper sulphate. At this stage, spiral heat exchangers can be added to recycle the rich acid’s low-grade heat which can then be used to pre-heat the lean acid coming back from solvent SX.
In the EW process, heat exchangers delivery optimum heat recovery by recovering low grade heat generated during the process and using it to preheat the rich electrolyte.
Why IWC?
Undertaking over 80% of all natural draught cooling tower refurbishment work in southern Africa, it’s easy to see why IWC remains Africa’s leading cooling tower specialist. Backed by industry expertise, IWC engineers world class thermal solutions for all cooling tower and heat exchanger needs.