For a 24 hour day, call IWC
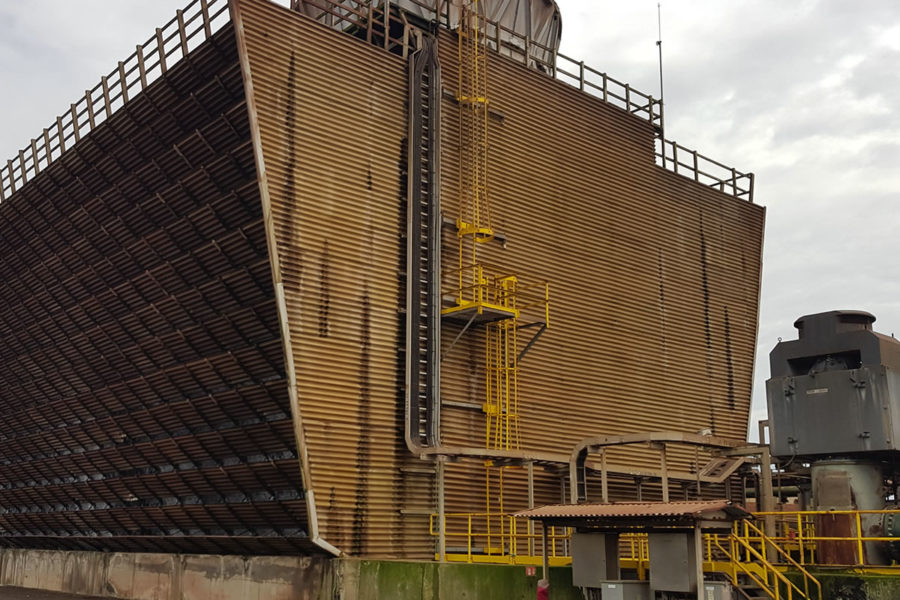
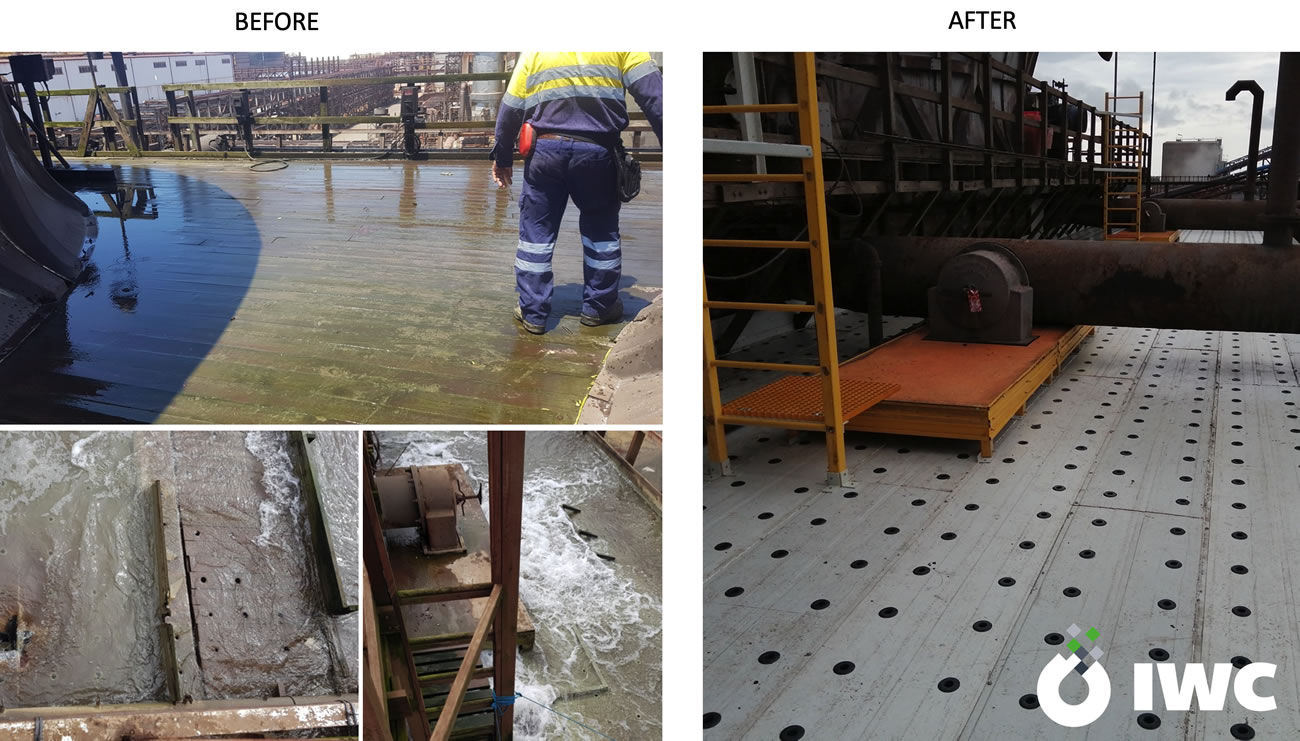
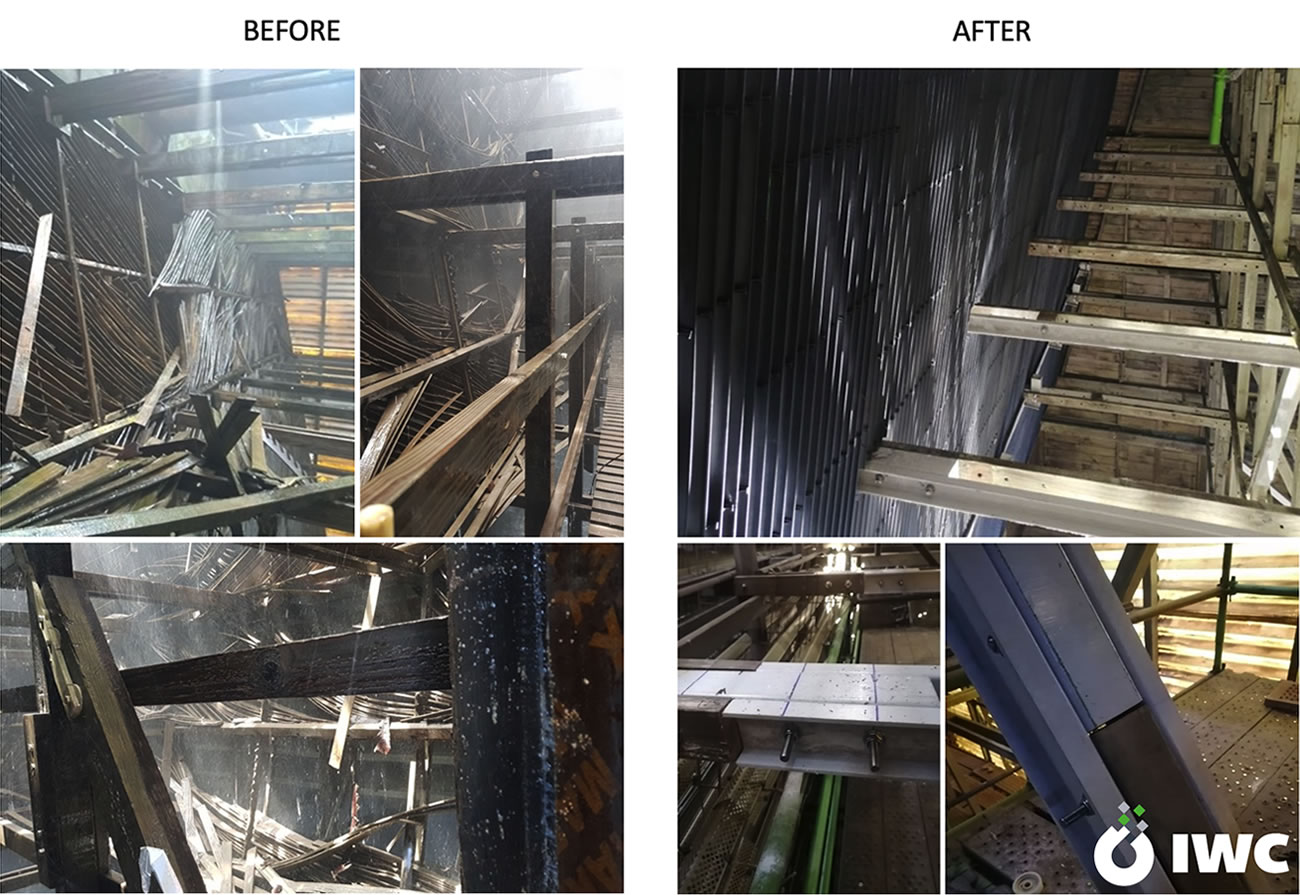
As one of the most ambitious industrial undertakings in the history of Madagascar, Africa, and the Indian Ocean Region, the Ambatovy Plant needs to runs 24 hours a day, so efficiency and performance is key, enter IWC.
IWC was recently approached by Ambatovy to provide assistance with two existing timber cooling towers that were not achieving the required thermal performance and in a poor state of repair.
Project Engineer, Gordon Beckett, conducted a site inspection and found that the two existing timber cross flow cooling towers were in a poor state of repair and not achieving the required thermal performance for their plants. Each cooling tower consists of 4 cells, one cooling tower for the (nickel) refinery cooling, and the other cooling tower for the plant utilities cooling.
The Issue
The existing timber slat drift eliminators had collapsed in many areas, causing excessive drift loss from the cooling tower which posed an environmental issue, as well as a safety hazard due to wet slippery surfaces. The excessive water losses from the cooling system results in poor thermal efficiency. Another noticeable impact of the excessive drift loss was corrosion on the adjacent plant and equipment
The water distribution deck on top of the cooling tower was also unsafe and in poor state of repair, with many cracks and damaged timber causing uneven water distribution over the cooling tower fill zone. The existing timber structure also showed numerous areas of concern with some damaged, rotten columns and beams.
Our Solution
After identifying all the issues on both cooling towers, we set out to make the required repairs. Our recommendation was to replace all the existing timber drift eliminators with new PVC drift eliminators which are more suited to long term corrosive environments. We implemented a suitable methodology of replacing the damaged components to ensure the structural integrity of the cooling tower was maintained.
The new PVC drift eliminators were supplied with stainless steel tie rods, including a new GRP support system secured to the existing timber structure. The water deck was replaced with GRP deck boards, as well as the replacement of 50% of the timber support structure with new GRP beams and stainless steel fasteners.
New GRP access ladders and platforms were installed on each water deck, and ad-hoc repairs to the timber structure were carried out, replacing damaged / rotten timber members with GRP sections where required.
An IWC qualified supervisor was on site to oversee the stripping and erection activities to ensure all work was carried out safely in accordance with our specifications and requirements. The labour and scaffolding for the work was provided by our client sub-contractors.
Why IWC?
We strive to design and implement thermal solutions that have a lower environmental impact by targeting a reduction in water use, energy use and carbon emission.
We achieve this by being highly consultative with all our clients, focusing on technical operation, capacity building, quality manufacturing and implementation.
IWC is one of the only companies globally to offer a vast range of product offerings, providing our customer base with bespoke engineered thermal solutions.