On-Line Refurbishment of a Natural Draught Cooling Tower
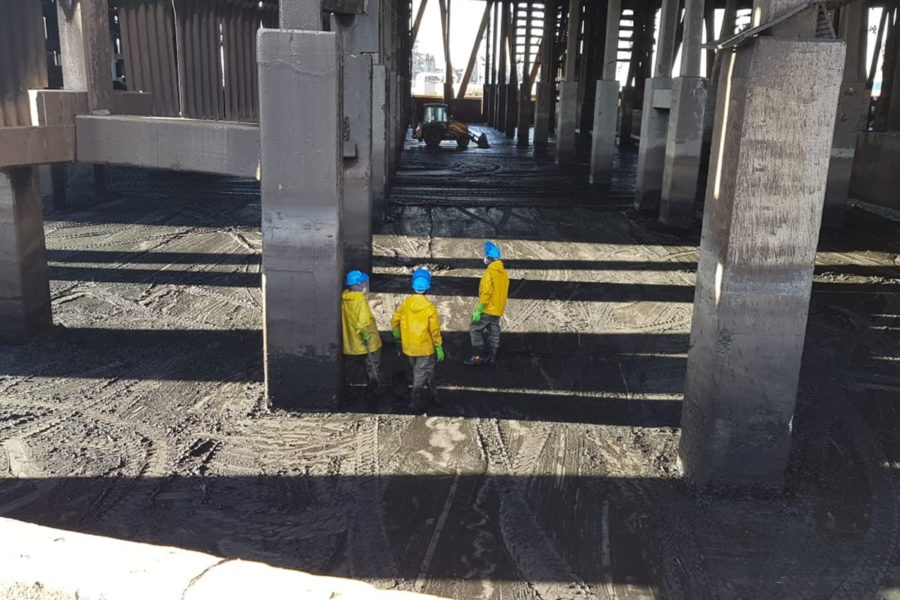
Late afternoon in December 2017, two concrete pre-cast beams collapsed in a large natural draft cooling tower. Consequently, approximately 70% of the splash grid fill collapsed catastrophically and fell into the basin thereby significantly reducing the efficiency of the cooling tower. This cooling tower is one of four in use in a large Petrochemical Complex constructed in South Africa and is critical to the plant throughput and efficiency.
The cooling tower in question is one of two natural draught cooling towers that form part of a cooling system that is designed to cool water from 42°C to 29°C, with a temperature range of 13°C. After the collapse, the re-cooled water temperature from the cooling tower was in excess of 35 °C, significantly impacting a multimillion Dollar production facility resulting in massive financial losses for the operator.
Due to the requirement for plant wide maintenance, a 14 day Shut Down was scheduled. This Shut Down signaled the start of the site works.
The works consisted of the removal and refurbishment of the fallen fill and existing support wires from the cooling tower basin. The removal and replacement of the two fallen concrete beams, replacement/repairing of all damaged concrete structural elements, replacement of damaged wind baffles, cleaning and removal of debris from the screens in the pump suction during the execution of the project and installing new replacement splash grid fill.
By the time the basin cleaning had been completed, 3 260 000 kg of material and sludge had been removed and disposed of at an approved landfill site.
The depth of sludge present in the basin made the choice of equipment used critical. Ultimately, it was decided to clear an area and construct a large ramp made from an ash/dolomite mix in order to drive earth moving equipment into the basin, between the shell supporting columns, to remove the debris.
With the plant shut down complete the cooling tower basin was refilled and the tower was put back into service. This however left us with the challenge of working on a live cooling tower. Working over a live cooling tower basin has its challenges, particularly when the topmost layer of fill is to be installed 13m above the water line.
For this project the use of a pontoon raft system was proposed. No references could be found to demonstrate that this has been successfully done to this order of magnitude i.e. scaffold height and area. Industrial Water Cooling, together with their Client, decided to undertake testing to establish the viability of the proposed pontoon raft at the required scaffold height and imposed loading.
The 20% portion of the cooling tower to be isolated was split into two discreet sections (10% of the tower area) and a pontoon raft built to cover the area. The pontoon raft was used as the base for construction of scaffolding and proved to be a safe and cost-effective method for obtaining access to the cooling tower internals.
In a previous refurbishment project isolation, valves were fitted to the distribution system. This made use of Industrial Water Cooling’s patented isolation methodology and the valves installed were used to isolate the areas needed to allow the refurbishment process to continue.
With the fill replacement complete, the re-cooled water temperature from the cooling tower was successfully reduced to a level close to the design point. Some critical design modifications were made to the fill design to reduce the impact of any potential failures in the future. All in all, a very successful project with great learnings and outcomes thanks to teamwork and partnership with our Client.