New Build Cooling Towers for India
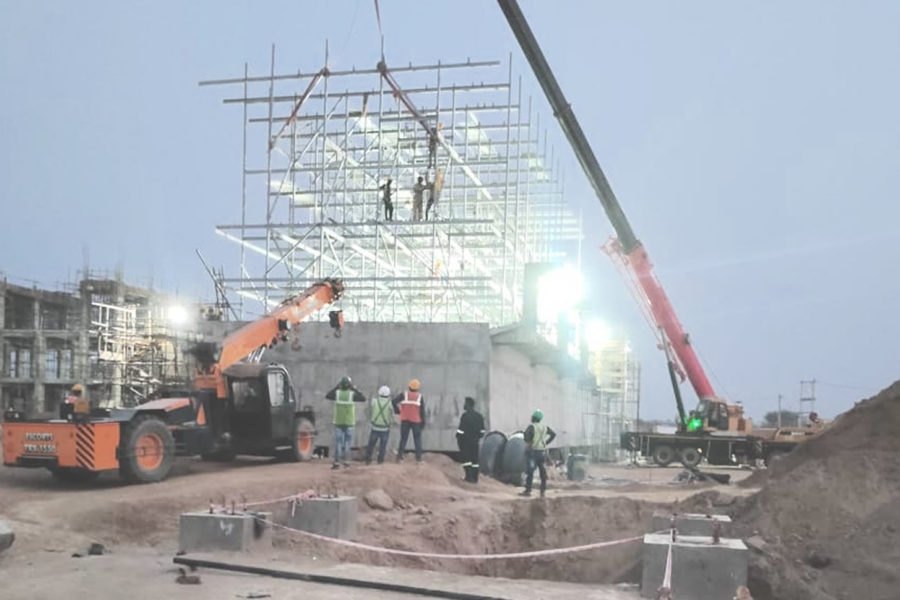
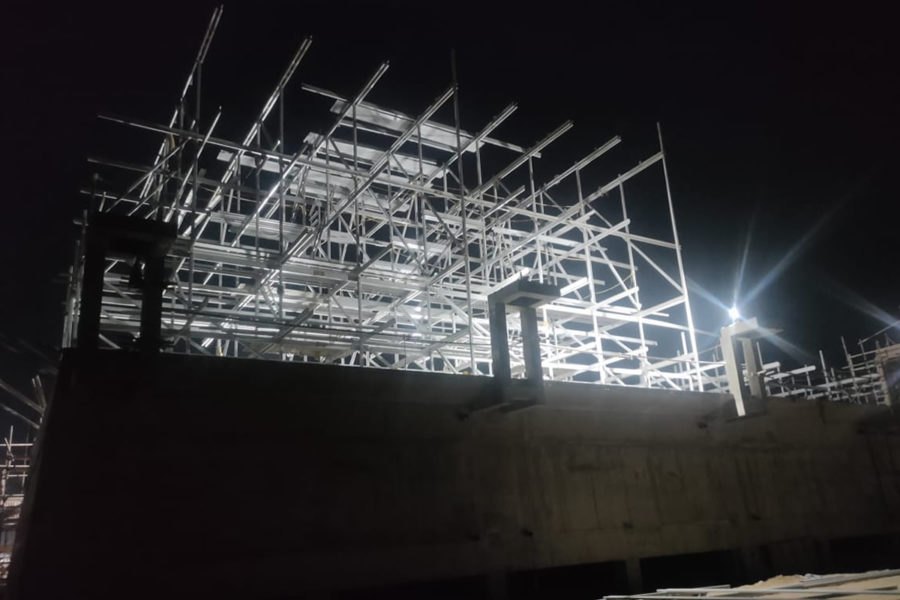
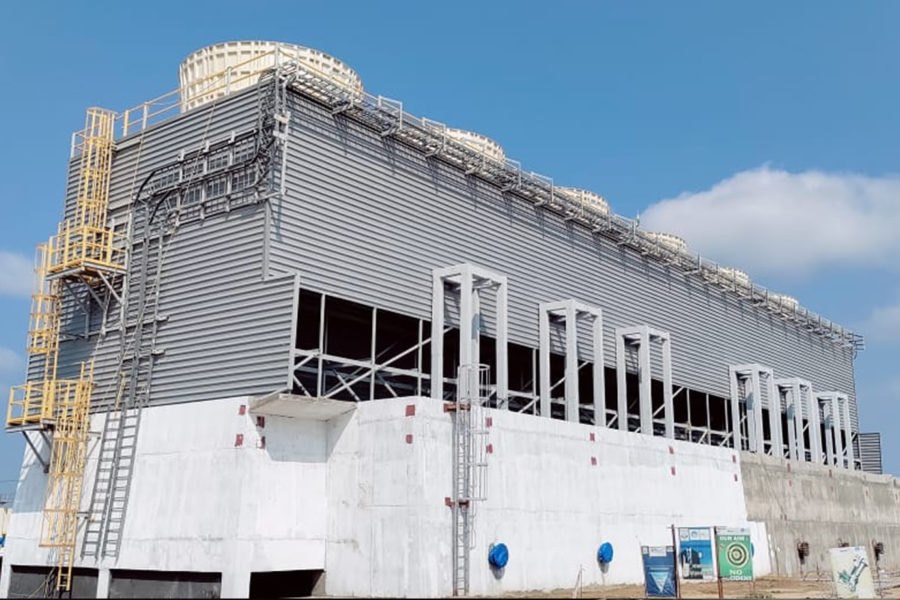
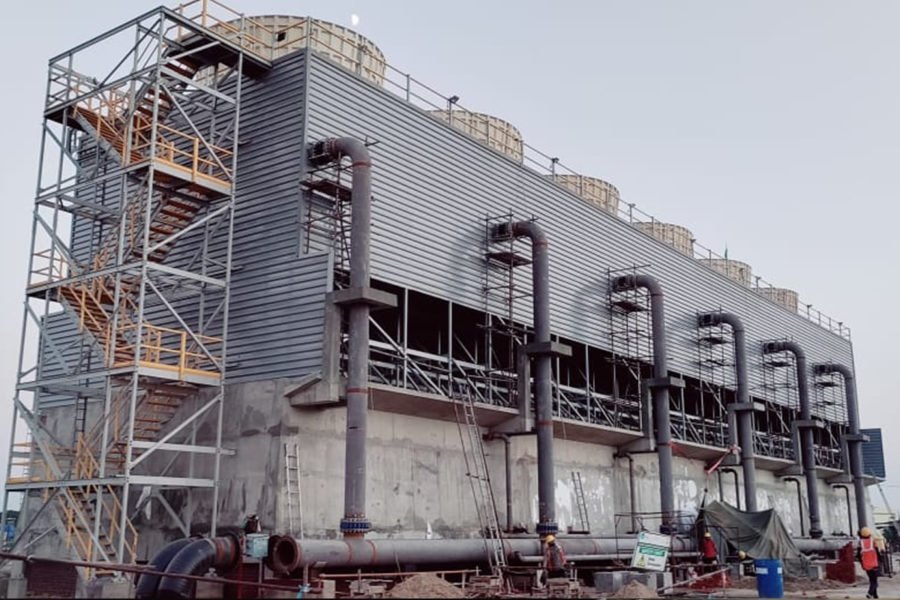
IWC Subsidiary, AS Cooling Technologies completes new cooling tower project for India’s first 2G Ethanol Bio-refinery in Bathinda.
The new build cooling tower project is for Hindustan Petroleum Corporation Limited’s 2G Ethanol plant. This initiative has been initiated by the Government of India to aid in the production of ethanol to be blended with petrol, to reduce the countries dependency on imported crude oil. The Government of India has set a target to achieve 20% ethanol blended petrol by the year 2025.
The proposed capacity of the plant will be 100 kilolitres of ethanol per day and may use sugarcane, biomass and other agricultural residues like rice-straw, wheat stubble and maize residue for the production of ethanol. It will also help in reducing CO2 emissions from the paddy straw, which is currently burnt after harvesting.
The bio-refinery will also produce about 32,000 tonne of bio-fertiliser per annum which can be used as a soil nutrient. Apart from this, the plant will also yield bio-CNG, which can be used as fuel for cooking
The project will also significantly help in reducing CO2 emissions from the paddy straw which currently is being burnt after harvesting.
Ethanol blending in petrol increases the oxygen content in fuel and ensures 100% clean combustion of petrol, thereby reducing vehicle exhaust emissions and thereby protecting the environment. Aside from this, ethanol blending can also go a long way in reducing the import burden of petroleum, saving foreign exchange and providing income for local farmers.
AS-CTI completed the project within 18 and the broad scope of work included design, engineering, procurement, supply, inspection and delivery to site.
We were also responsible for the civil construction, erection, pre-commissioning, commissioning and performance testing of the new 6 cell FRP cooling tower along with concrete basin, piping, side stream filters, chemical dosing system, electrical and instrumentation. Flow rate per cell is 1650 m3/hr and the total installed capacity is 9900m3/hr.