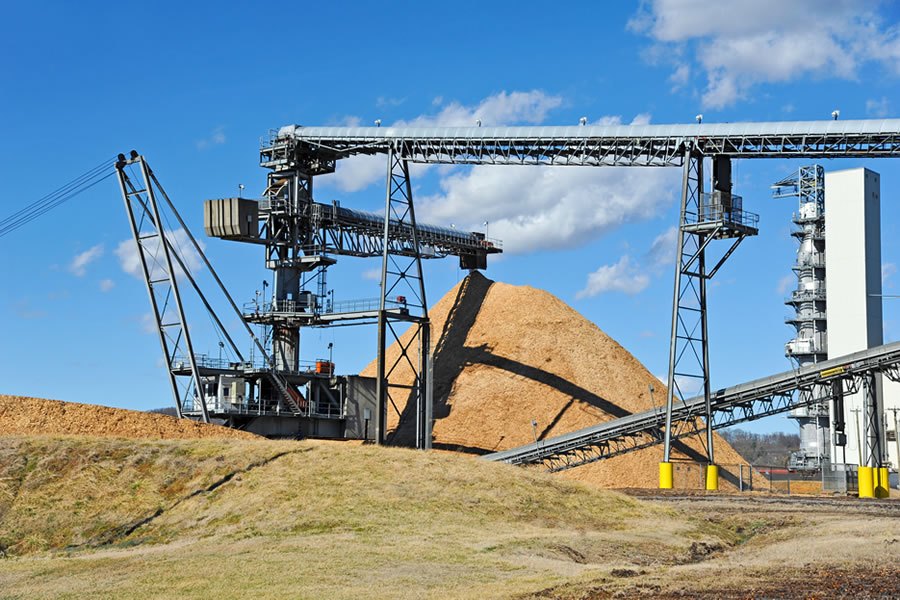
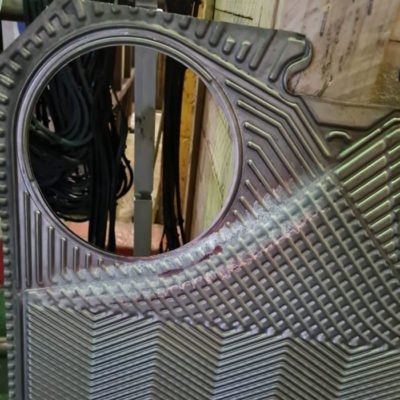
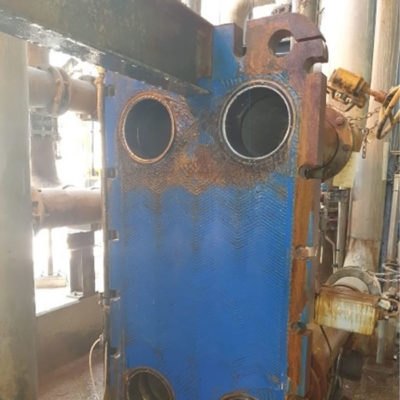
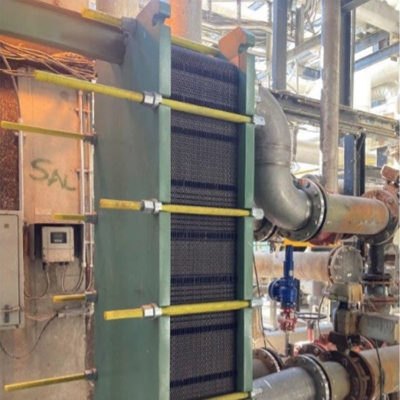
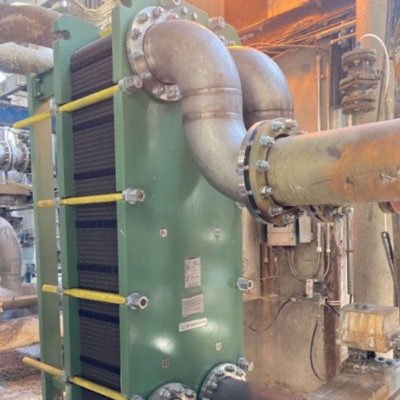
Requirement
Service and subsequent replacement of a Semi-Welded PHE in Chlorine Dioxide/water solution process to increase the thermal performance of the plant.
Solution
In December 2020 we were contacted by the maintenance manager at a pulp & paper mill to service a Sondex SW59 PHE. Upon examination we found that all the titanium cassettes (semi-welded) were compromised due to cracks near the welds which are close to the ports (see pic 1).
We also established that the frame of the PHE was in a poor condition (see pic 2) and our recommendation was to purchase a new plate heat exchanger since a new plate pack and refurbishing the frame, would be almost the same price.
The client approved the purchase of a new heat exchanger, however due to budgeting constraints the order was placed with another supplier in February 2021. In April 2021 the project manager contacted us to advise that the other supplier was no longer able to supply the heat exchanger and enquired if we could assist in supplying the new PHE within the same time frames as the other supplier. After discussions with Shineheat, our partner and preferred supplier for Plate Heat Exchangers, we committed to deliver within the tight timelines originally agreed to by the other supplier.
Process Data Sheets and Drawings were submitted to the client and after approval, the manufacturing commenced. The new PHE (AT200MW) would also have titanium semi-welded plates and Viton gaskets, but since the “center to center” dimensions of the connections were different to the old SW59 PHE, we were also required to fabricate two titanium and two 316SS spool pieces. These spool pieces were also ordered from Shineheat.
A weekly progress report was forwarded to the client to keep them informed on the manufacturing of the new AT200MW and spool pieces. The PHE was manufactured in record time and all quality requirements were met. The unit was then disassembled and packed in wooden crates to facilitate air freight of the PHE.
The crates were airfreighted and delivered to our workshop in Richards Bay where our site manager assembled the PHE and delivered the complete assembled and pressure tested heat exchanger to site, 4 days ahead of the promised delivery date. The heat exchanger was installed and commissioned successfully and is operating as per design specifications. The new operational heat exchanger saves our client a significant amount of revenue per month.
The client was thrilled with the speedy execution of the project and the weekly progress updates during the manufacturing process.