Refinery 113 – Back in business
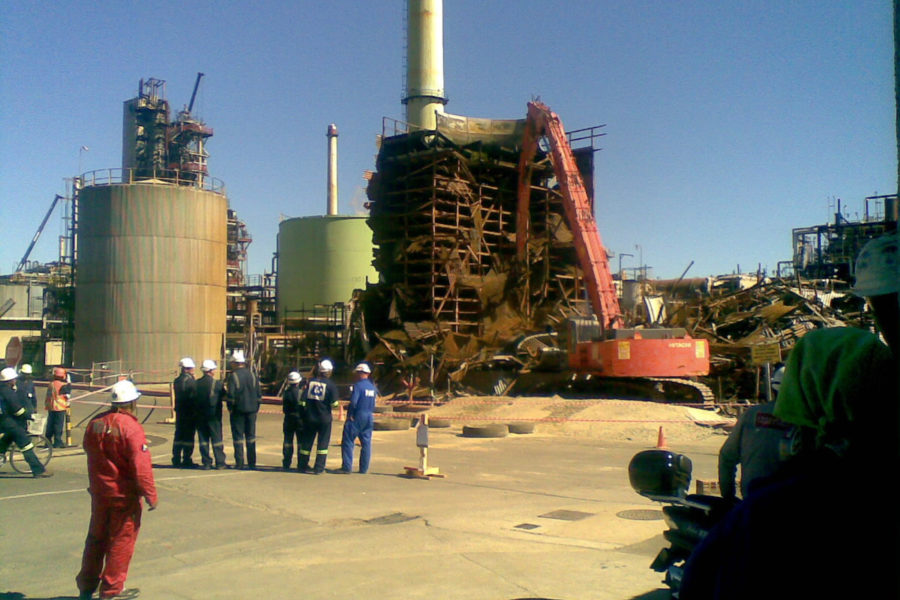
Cooling tower replacement project
IWC was approached by a petrochemical refinery in Cape Town to inspect their current cooling tower which was in extremely poor state of repair and not providing the cooling requirements for their plant. IWC was called in to save the day.
After a site inspection and consultation, it was agreed to replace the existing timber cooling tower with a pultruded fiberglass (GRP) structure. Additional requirements included new water distribution piping, new mechanicals and a new access staircase.
The project objective was to ensure that the new cooling tower would meet the very specific thermal duty for the plant – Water flowrate – 1600 mᶾ/hr, Cooling Capacity – 40.8 MW and Number of cells – two
The challenge we faced was to ensure the safe demolition of the existing cooling tower. Due to the unstable timber structure, with several rotten timber components and some internals having already collapsed, it was simply too risky to carry out a conventional approach by stripping items by hand. To negate these risks mechanical demolition equipment (with their own risks) was used.
We also had to ensure that the adjacent plant and concrete basin was not damaged during demolition activities. To prevent this, careful detailed planning, competent machine operators, safety watchers and a systematic approach were key to the success.
The plant had to be shut down for a short period for the duration of work required. The new cooling tower structure was pre-assembled, prior to the commencement of the shutdown, into four sections in an open area near the cooling tower. A large crane, with extended boom, was then used to lift and install the sections into place after demolition and clearing of the concrete basin. Once the new structure was securely in place our site teams commenced with the installation of the internals, cladding and mechanicals. Our site teams worked 12 hour shifts in order to meet the required deadline for plant start-up.
With the correct approach to safety, quality, engineering, planning and project management, IWC could confidently take on this project despite the high safety risks involved and the short project duration. Our proactive and dynamic approach ensured another successful project delivered under budget and within the prescribed time.
Contact us to see how we can assist with your cooling tower refurbishment project.